Fast jeder hat bereits daraus getrunken oder welche davon in seinem Schrank – Kristallgläser von Ritzenhoff. Als einziger Glashersteller Europas bietet das Familienunternehmen am Stammsitz in Marsberg im Sauerland alles, was für die Entwicklung und Produktion eines Trinkglases notwendig ist, aus einer Hand. Das Spektrum reicht vom Entwurf über Produktion und Veredelung bis zur Lager- und Lieferlogistik. Die Fertigung ist eine der modernsten Glasproduktionsstätten Europas.
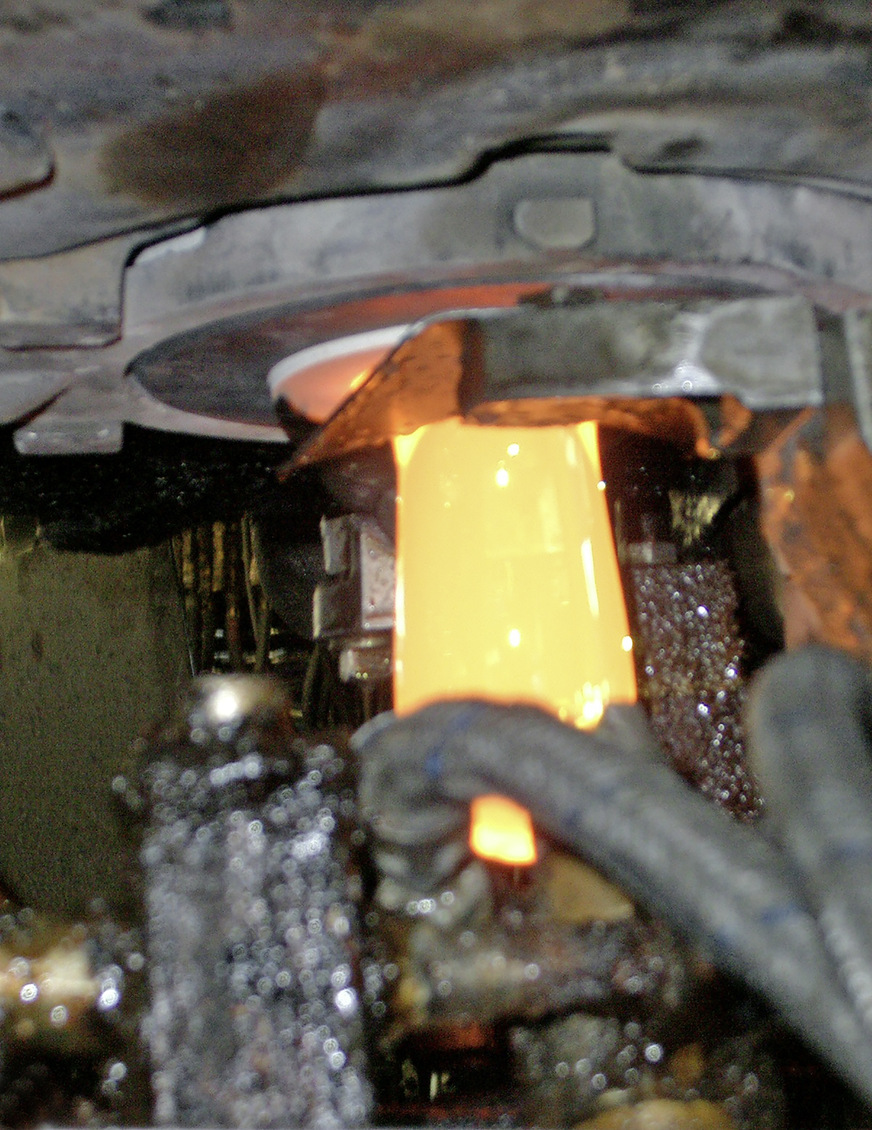
Bild: Ritzenhoff
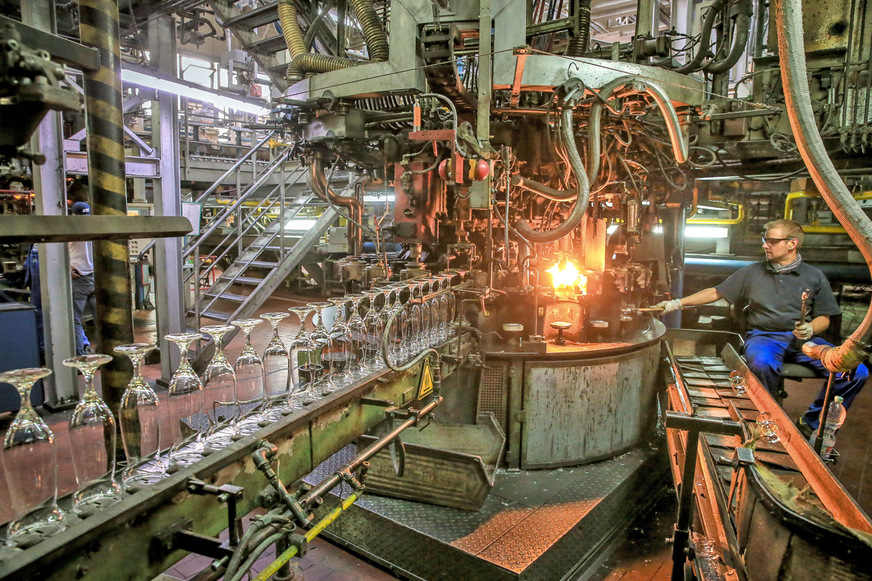
Bild: Ritzenhoff/Joern Hannemann
Von der Rohstoffaufbereitung zum fertigen Trinkglas
Beim Herstellungsprozess wird zunächst das Gemisch aus Quarzsand, kalzinierter Soda, Kalk, Pottasche, Kalisalpeter und eigenem Recyclingglas bei 1500 °C zum fertigen Glas aufgeschmolzen. Das flüssige Glas wird in Tropfen portioniert und während des Erkaltungsprozesses in Form gebracht – als Kelch geblasen, zu Stielen gepresst, per Laser geschnitten, zusammengesetzt und verschmolzen. Auf den vier parallel laufenden Glasproduktionslinien werden so täglich bis zu 65 Tonnen an flüssigem Rohglas zu 140 000 Gläsern verarbeitet.
Exakte Übergabekühlung
Die Glasschmelze kommt mit 1150 °C aus der Schmelzwanne an die Schneidanlage, wo ein bis zu 500 Gramm schwerer Tropfen abgeschnitten und an die Glasblasmaschine übergeben wird. Den Transfer zur Blasmaschine übernimmt die sogenannte „Übergabe“. Ein Anlagenteil mit besonderen Anforderungen: Exakt berechnete Kühl- und Vakuumkanäle müssen den Transport des Tropfens gewährleisten, die Temperatur des Tropfens regulieren und den Tropfen rechtzeitig abblasen, um diesen in die Blasmaschine einzulegen.
„Das Kühlwasser für die Übergabe an die Blasmaschine muss konstant mit einer Temperatur von 19 °C zur Verfügung stehen und heizt sich während des Vorgangs bis auf 27 °C auf“, erklärt Denim Steinert, Ingenieur für Energietechnik und Energiemanagementbeauftragter von Ritzenhoff. „Für die vier Produktionslinien wird an dieser Stelle eine Kälteleistung von 80 kW in der Spitze benötigt. Die Anlagen laufen 24 Stunden an 365 Tagen im Jahr; man kann sich also vorstellen, welche Bedeutung der Betriebssicherheit und Energieeffizienz des Kühlsystems beigemessen wird“.
Langjähriger Partner für Kälte und Druckluftaufbereitung
Die Zusammenarbeit zwischen Ritzenhoff und MTA Deutschland währt bereits seit mehr als 20 Jahren. Bernd Schmidt, Leiter Drucklufttechnik bei MTA, betreut Ritzenhoff nicht nur in allen Fragen rund um das Thema Druckluftaufbereitung, sondern war auch maßgeblich an der Auslegung des ursprünglichen Kühlsystems beteiligt. Das in 1999 in Betrieb genommene System bestand aus einer innen aufgestellten Kältemaschine und einem externen Rückkühler, der zusätzlich zur freien Kühlung genutzt wurde. Die Gründe zur Modernisierung des Kühlsystems lagen auf der Hand: neben Alter und Kapazitätsgrenze der 125 kW Bestands-Kältemaschine standen Gesamtwirkungsgrad und Betriebssicherheit im Fokus der Betrachtungen.
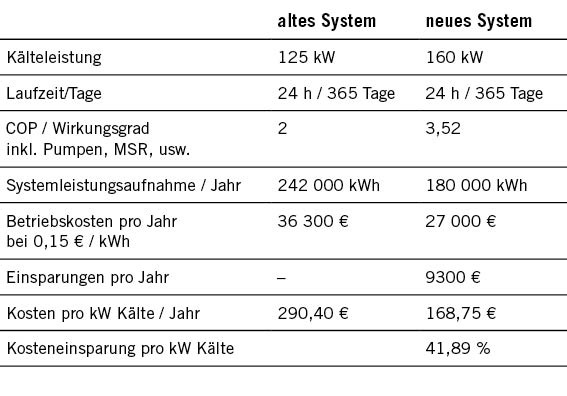
Ermittlung der erforderlichen Kälteleistung
Die Auswertung der Jahrestemperaturen, aufgezeichnet in den letzten fünf Jahren, ergab eine Spitzenlast-Auslegung bei 40 °C Außentemperatur. Hieraus leitete sich folgender Kälteleistungsbedarf ab:
Die geforderte Kühlleistung summiert sich auf 145 kW, zuzüglich Leistungsreserve für potenzielle Erweiterungen und extreme Lastzustände.
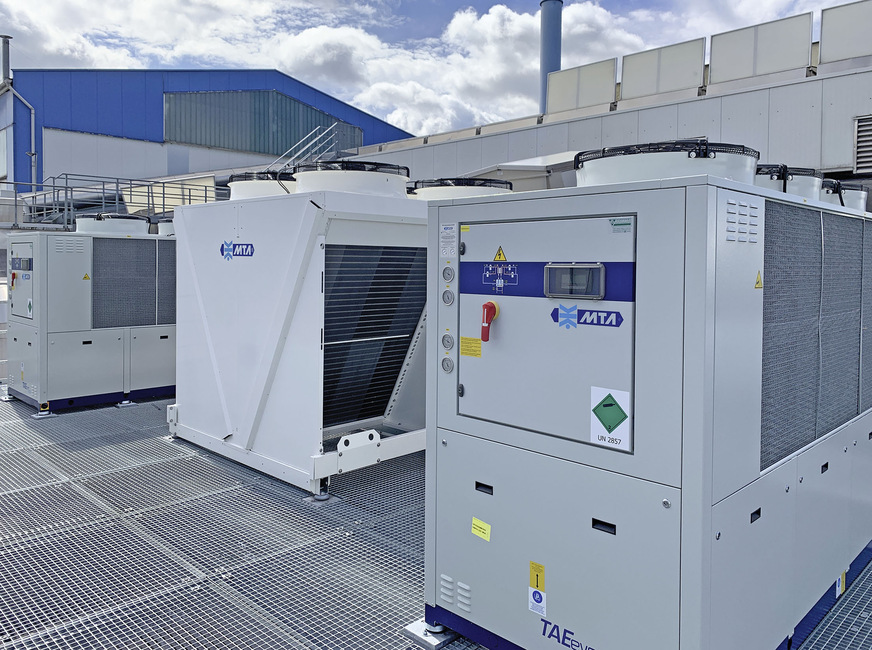
Bild: MTA
Freie Kühlung, Spitzenlastabdeckung und 100 Prozent Redundanz
Das jetzt installierte MTA-Kühlsystem besteht aus zwei in Außenaufstellung betriebenen Kaltwassersätzen vom Typ TAEevo Tech 802, die bei niedrigen Außentemperaturen durch das Freikühlmodul RWD 163 entlastet werden. Jeder Kaltwassersatz liefert eine Nenn-Kälteleistung von 160 kW bei 40 °C Außentemperatur, wobei der Aufbau dem Prinzip der Serienschaltung folgt. Bei Außentemperaturen bis 14 °C wird der gesamte Wärmeeintrag über den Freikühler abgeführt. Bei steigender Temperatur übernimmt Kaltwassersatz Nummer 1 und regelt so lange selbstständig seine Leistungsstufen, bis der vorgegebene Sollwert der Kühlwassertemperatur überschritten wird und Kaltwassersatz Nummer 2 sich automatisch zuschaltet. Auf einer eigens hierfür gebauten Stahlbaukonstruktion sind die Kaltwassersätze und der Freikühler in luftiger Höhe installiert, um sowohl die Wärmeabfuhr bei den luftgekühlten Kaltwassererzeugern, als auch eine optimale Anströmung mit kalter Außenluft für die freie Kühlung zu gewährleisten. Kaltwassersätze und Freikühler kühlen so von 20 °C am Kühlwasser-Eintritt auf eine Vorlauftemperatur von 13 °C und fahren auf einen in der Technikzentrale zur Systemtrennung installierten Plattenwärmetauscher. Diese Trennung ist zum einen aufgrund der unterschiedlichen Temperaturniveaus erforderlich, dient aber auch dem Betrieb der außen aufgestellten Anlagen mit einem Wasser-Glykol-Gemisch zur Frostfreiheit. Auf Prozessseite wird in zwei 1500 Liter-Speichertanks Kühlwasser mit der erforderlichen Systemtemperatur von 19 °C bevorratet; frequenzgeregelte Pumpen sorgen für die bedarfsgerechte und energieeffiziente Umwälzung.
Intelligente Steuerung
Der von MTA speziell für diese Anwendung gelieferte Regler zur automatischen Betriebs- und Störumschaltung betreibt die beiden Kaltwassersätze lastabhängig. Dabei findet eine gleichmäßige Verteilung der Betriebsstunden auf beide Geräte statt. Im Störfall bei einer Anlage findet eine automatische Umschaltung auf das intakte Gerät statt. Darüber hinaus enthält der Schaltschrank eine Temperaturüberwachung des zu kühlenden Wassers, die dazu genutzt wird, die beiden Kaltwassersätze bei besonders extremen Lastzuständen für eine höhere Leistungsausbeute in Parallelbetrieb zu schalten (Notbetrieb). Alle Parameter zur Regelung der Kühlwasser-Rückkühlung werden vom eigens hierfür von Ritzenhoff entwickelten Prozessleitsystem verarbeitet.
Fazit
Durch den Austausch des mehr als 20 Jahre alten Kühlsystems durch die neuen MTA Prozesskühler mit intelligent gesteuerter Freikühlung konnten nach Inbetriebnahme am 1. Juli bisher folgende Leistungsdaten ermittelt werden:
Außentemperatur)
(Bedingt durch die Corona Pandemie waren zum Zeitpunkt der Aufzeichnung nur zwei der vier Produktionslinien in Betrieb.)
Bei Ritzenhoff sorgt das Ergebnis rundum für zufriedene Gesichter. „Mit einer elektrischen Leistungsaufnahme von 15 kW bei einer abgerufenen Kälteleistung von 46 kW für zwei Produktionslinien inklusive aller Nebenverbraucher sind unsere Erwartungen vollauf erfüllt“, betont Energiemanager Steinert.
„Und bei 20 °C Außentemperatur ist das Potenzial der freien Kühlung ja nicht einmal annähernd ausgeschöpft. Unsere Berechnungen haben ergeben, dass der Freikühler zu 70 Prozent des Jahres die Dauerlast übernehmen kann und durchaus auch an Sommertagen in den frühen und späten Stunden zur Vorkühlung zum Einsatz kommt. Das führt zu einer Einsparung von mehr als 62 000 kWh, wobei die effektive Kälteleistung mit jetzt 160 kW auch noch 30 Prozent über der alten Anlage liegt.“
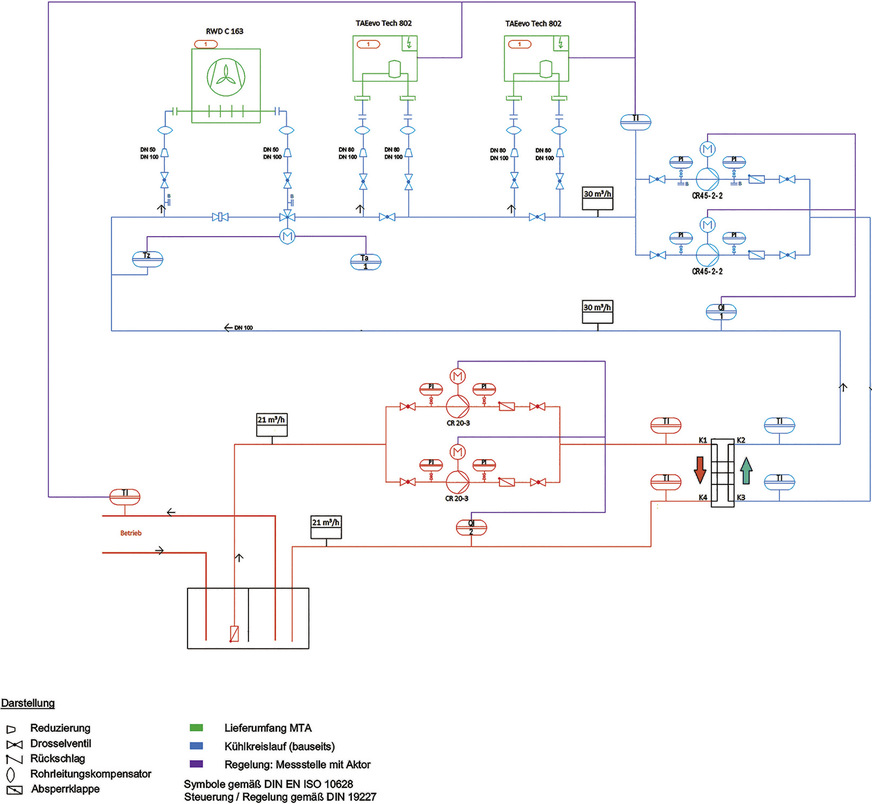
Bild: MTA
MTA S.p.A. und MTA Deutschland GmbH
MTA produziert und vertreibt seit 35 Jahren Industrie-Kühlsysteme zur Prozesskühlung, Klimatisierung und Druckluftaufbereitung.
In den drei norditalienischen Produktionsstätten Tribano, Conselve und Bagnoli, mit einer Produktionsfläche von insgesamt 58 000 m², werden jährlich mehr als 22 000 Kaltwassersätze, Freikühler und Drucklufttrockner gefertigt.
Weltweit ist MTA mit aktuell 440 Beschäftigten in über 80 Ländern vertreten.
MTA Deutschland mit Hauptsitz in Nettetal am Niederrhein betreut seine Kunden bundesweit mit einem 60-köpfigen Vertriebs- und Serviceteam und die interne Engineering-Abteilung entwickelt maßgeschneiderte
Kühlsysteme für Industrie und Gewerbe.